


The 8th Power Battery Application International Summit (CBIS2023), hosted by the China Chemical and Physical Power Source Industry Association and Battery China Network, will be held in Shanghai from November 28th to 30th. The theme of this summit is "Service·Cooperation·Win-win - Embracing the 'New Globalization' Era". Experts and industry representatives from various fields of the power battery and energy storage battery industry chain at home and abroad will gather together to discuss The development of power batteries and energy storage batteries in the "new globalization" era
The rewritten content is: Meeting scene
At the special theme forum of "Digital Intelligence Empowers the New Energy Battery Industry" on the afternoon of the 29th, Chen Yao, Sales Director of Lingyun Optical Technology Co., Ltd., delivered a speech entitled "Empowering Extreme Intelligent Manufacturing, Laying out the Future of the Industry" ’s keynote speech, shared with the guests ’s understanding of the new requirements of intelligent manufacturing in the “TWh” era and the products and solutions launched by Ling Yunguang with machine vision AI as the core.
Ling Yunguang Sales Director Chen Yao "Empowering extreme intelligent manufacturing and laying out the future of the industry"
Looking at the current application status of machine vision online quality inspection, the application scenarios of machine vision online quality inspection are becoming more and more abundant, but it still faces difficulties such as high risk of defect outflow, lack of obvious labor saving effect, and difficulty in realizing the value of data. The reason is that Imaging system design is not standardized, production management is not standardized, and service is not standardized.
The lithium battery industry that pursues extreme manufacturing requires intelligent production, intelligent detection, and intelligent management, so visual inspection must be more accurate, more reliable, and smarter. Combining more than 20 years of experience in machine vision, Ling Yunguang gave his own answer.
The importance of implementing online quality inspection standardized lithium electrode sheets is to ensure product quality and production efficiency. By establishing standardized quality inspection processes and accurate testing methods, the manufacturing process of electrode sheets can be effectively monitored, and potential quality problems can be discovered and resolved in a timely manner. At the same time, standardized quality inspection methods can also improve production efficiency, reduce costs, and bring more competitive advantages to enterprises. Therefore, the implementation of online quality inspection standardization is an inevitable trend in the battery manufacturing industry and a key measure to enhance corporate competitiveness
Imaging system: high and low dynamic imaging, accurate detection of virtual edges
A truly useful visual inspection solution requires imaging system design based on full study of the inspection object.
Taking lithium battery pole pieces as an example, there is a big difference between high reflectivity and low reflectivity, and the sensitivity to spectral response is different. In order to complete the inspection of the electrode plate coating area and the blank area at the same time, the traditional inspection solution requires the addition of new stations, which increases the hardware cost and makes the system more complex. Lingyun Optical has innovatively launched a high-low dynamic imaging solution to achieve precise capture and measurement of virtual edge defects, effectively improving efficiency and increasing single-point reliability by 50%.
The content that needs to be rewritten is: virtual edge detection
At the same time, for defects that are not obvious in imaging such as bubbles and wrinkles, Lingyunguang uses a compact design to completely present the defect shape with the optimal imaging solution and achieve accurate classification and classification of defects.
Algorithm system: offload three steps to GPU to reduce load
The traditional process of online quality inspection usually uses the CPU for positioning measurement, and then uses the GPU for appearance inspection and defect classification. This results in overloading the GPU, and coupled with the demands of deep learning, the GPU is even more overwhelmed
Ling Yunguang makes full use of the computing power of the original capture card through three-step diversion, significantly reducing the dependence on the graphics card and reducing the burden on the GPU.
Three-step diversion: Put simple convolution and streaming calculations into the capture card of the self-developed camera for processing - Put logical calculations and simple feature calculations into the CPU for processing - Put the classification and grading of defects into Go to the GPU for processing.
System modularity: high ease of use, low cost
As customers’ requirements for product quality increase and labor costs soar in the overseas environment, the ease of use of equipment has become particularly important.
Based on this, we have standardized and modularized the design of the testing equipment. The integrated design of the camera head and light source enables plug-and-play, significantly improving imaging system consistency and reducing maintenance costs.
Star products have soul
In the development process of multiple new products, Ling Yunguang will use his accumulated experience in imaging system design, algorithm design, and system modular design
Lithium battery burr online full inspection system
——Pursue high speed and high precision, taking into account both
Lingyunguang applies high-speed imaging technology to the field of pole piece burr detection. Combined with the independently developed optical system, it realizes adaptive focus tracking, improves the system depth of field, and achieves high-speed imaging with high resolution, large field of view, and large depth of field, stable and clear imaging at a speed of 150m/min, complete inspection of pole piece edge burrs, detection resolution 2μm.
Lithium battery square appearance inspection equipment
——Small and powerful, rest assured your first choice
It is the function of the lithium battery square appearance inspection equipment to conduct comprehensive quality inspection and defect removal of aluminum-cased batteries and coated batteries
In terms of imaging system, for the common blue film detection of square batteries, Lingyunguang has launched a self-developed 2.5D imaging system, which can accurately identify foreign objects and bubbles under the blue film through time-sharing stroboscopic multiple imaging , conduct re-inspection of defective products to prevent problems before they occur.
In addition, by optimizing the internal structure of automation components, optical detection components, etc., the square appearance inspection equipment subverts the common "one-line" route and innovatively uses the circular inspection path, successfully integrating the complete machine The floor space has been "downsized" to less than 7 square meters.
In the future, Ling Yunguang hopes to build a complete quality system for the industry, obtain more visual quality data from the end side, and make quality benchmarks more standardized and consistent; unify models and continue to unify defect learning at the edge end Distribution (for example, once a defect in a coating machine on the production line is discovered, other coating machines can obtain a unified model from the server.); finally, the entire quality analysis and decision-making system is built on the cloud. Realize the overall collaboration of terminal, edge and cloud, and make the data of industrial production digitalized, industrialized and intelligent.
The above is the detailed content of Machine Vision + AI | Empowering extreme intelligent manufacturing and laying out the future of the industry. For more information, please follow other related articles on the PHP Chinese website!
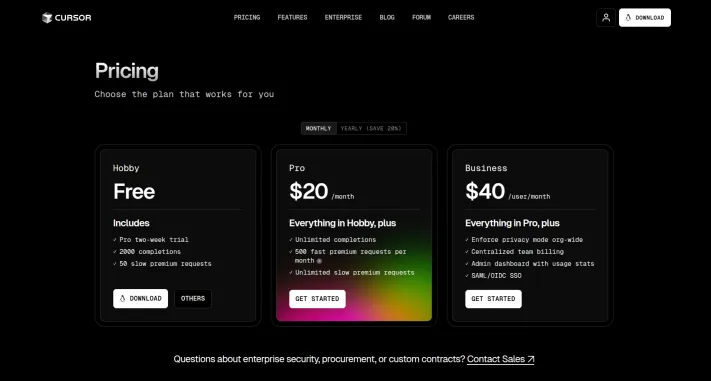
Vibe coding is reshaping the world of software development by letting us create applications using natural language instead of endless lines of code. Inspired by visionaries like Andrej Karpathy, this innovative approach lets dev

DALL-E 3: A Generative AI Image Creation Tool Generative AI is revolutionizing content creation, and DALL-E 3, OpenAI's latest image generation model, is at the forefront. Released in October 2023, it builds upon its predecessors, DALL-E and DALL-E 2
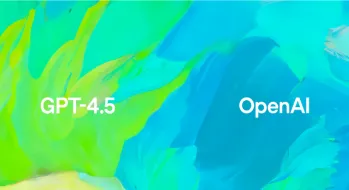
February 2025 has been yet another game-changing month for generative AI, bringing us some of the most anticipated model upgrades and groundbreaking new features. From xAI’s Grok 3 and Anthropic’s Claude 3.7 Sonnet, to OpenAI’s G
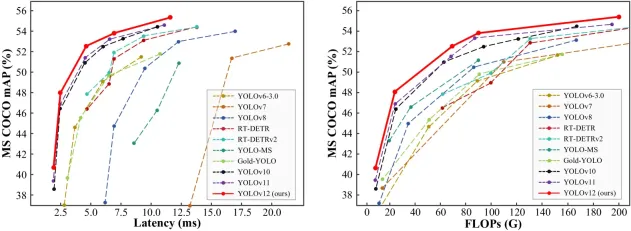
YOLO (You Only Look Once) has been a leading real-time object detection framework, with each iteration improving upon the previous versions. The latest version YOLO v12 introduces advancements that significantly enhance accuracy
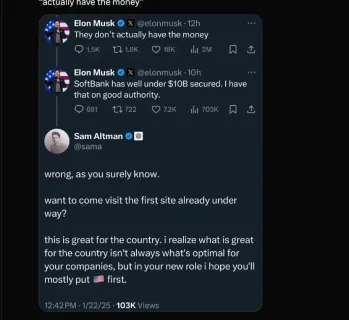
The $500 billion Stargate AI project, backed by tech giants like OpenAI, SoftBank, Oracle, and Nvidia, and supported by the U.S. government, aims to solidify American AI leadership. This ambitious undertaking promises a future shaped by AI advanceme
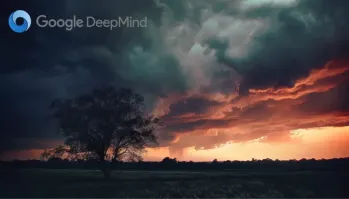
Google DeepMind's GenCast: A Revolutionary AI for Weather Forecasting Weather forecasting has undergone a dramatic transformation, moving from rudimentary observations to sophisticated AI-powered predictions. Google DeepMind's GenCast, a groundbreak
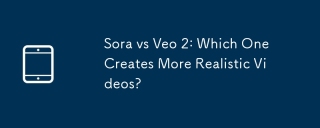
Google's Veo 2 and OpenAI's Sora: Which AI video generator reigns supreme? Both platforms generate impressive AI videos, but their strengths lie in different areas. This comparison, using various prompts, reveals which tool best suits your needs. T
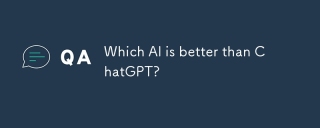
The article discusses AI models surpassing ChatGPT, like LaMDA, LLaMA, and Grok, highlighting their advantages in accuracy, understanding, and industry impact.(159 characters)


Hot AI Tools

Undresser.AI Undress
AI-powered app for creating realistic nude photos

AI Clothes Remover
Online AI tool for removing clothes from photos.

Undress AI Tool
Undress images for free

Clothoff.io
AI clothes remover

AI Hentai Generator
Generate AI Hentai for free.

Hot Article

Hot Tools

SublimeText3 Linux new version
SublimeText3 Linux latest version
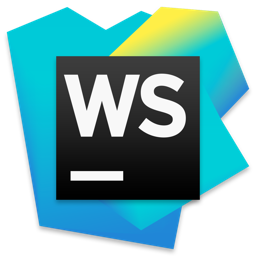
WebStorm Mac version
Useful JavaScript development tools
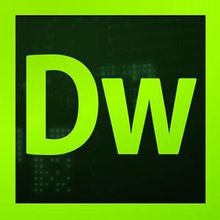
Dreamweaver CS6
Visual web development tools

SAP NetWeaver Server Adapter for Eclipse
Integrate Eclipse with SAP NetWeaver application server.

SublimeText3 Chinese version
Chinese version, very easy to use
